As 3D-printing methods continue to evolve, it’s not uncommon to see this method employed for various engineering projects, especially in the construction of affordable housing, structures, and schools.
In Ireland, a first-of-its-kind social housing project has been built from the ground up, using 3D printing as a time and money-saving solution.
In fact, it’s Europe’s first 3D-printed social housing project, fully compliant with international standards. In Grange Close, Dundalk, the three-unit terraced build is now a milestone achievement in eastern Ireland. It was created by Harcourt Technologies Ltd (HTL.tech) and assembled using COBOD’s BOD2 3D construction printer.
The unit is 3,550 square feet and is divided into three separate homes, each measuring 1,184 square feet.
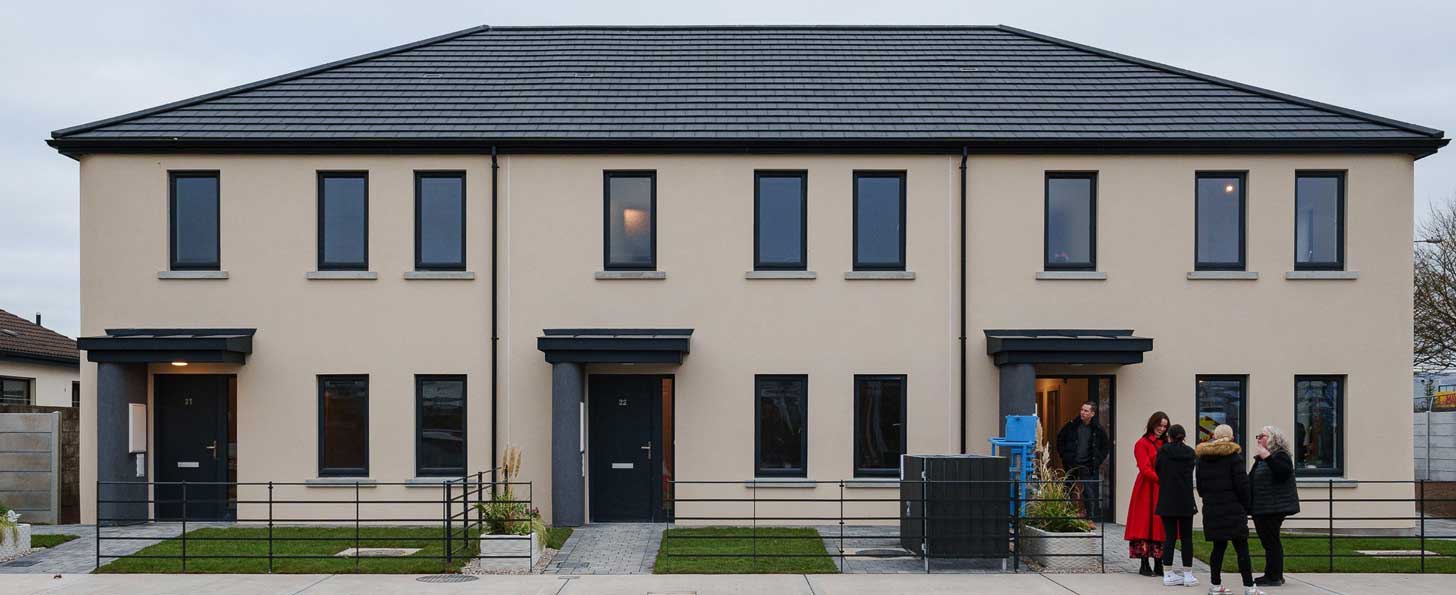
The use of this technology allowed for a 35% faster construction process, which took 132 days from start to finish. During that time, the 3D-printed superstructure itself was completed in just 12 printing days.
Conventional construction methods usually require more than 200 days, according to COBOD, meaning this method could be transformative in quickly scaling affordable housing options.
“Ireland’s housing crisis, driven by a decade of under-construction and rising demand, has reached critical levels, leading to widespread protests and influencing national elections,” HTL.tech shared in a press release.
“The rapid construction made possible by 3D printing offers a promising solution. The homes in Dundalk demonstrate how this technology can address housing shortages by dramatically reducing construction time and costs.”
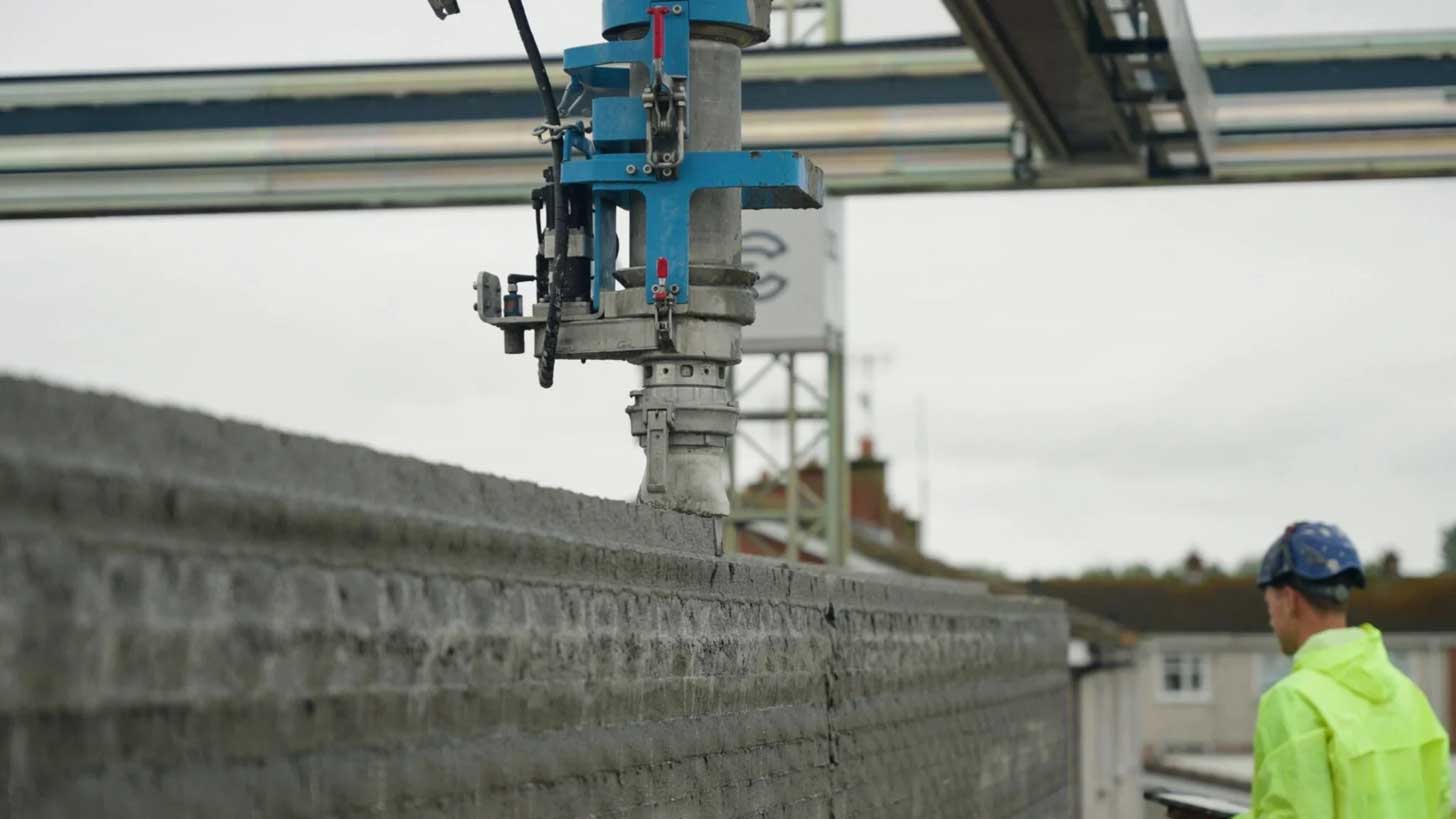
In the 132 days it took to go from initial site preparation to handing over keys to the client, builders say approximately half of the time savings came directly from 3D printing.
Additionally, during the project, COBOD upgraded the concrete hose of its printer, which increased its output by 40% and significantly increased the printing speed. With this upgrade, the company estimates that printing times for similar structures would be reduced to nine days instead of 12.
“We continue to improve our technology,” Henrik Lund-Nielsen, general manager and founder of COBOD International, said in a statement, “and although a hose update can be seen as a small step, the numbers from HTL.tech proves that it is not.”
Now, the client — a local housing council — will finish furnishing the homes and will rent them to social housing tenants at an affordable price.
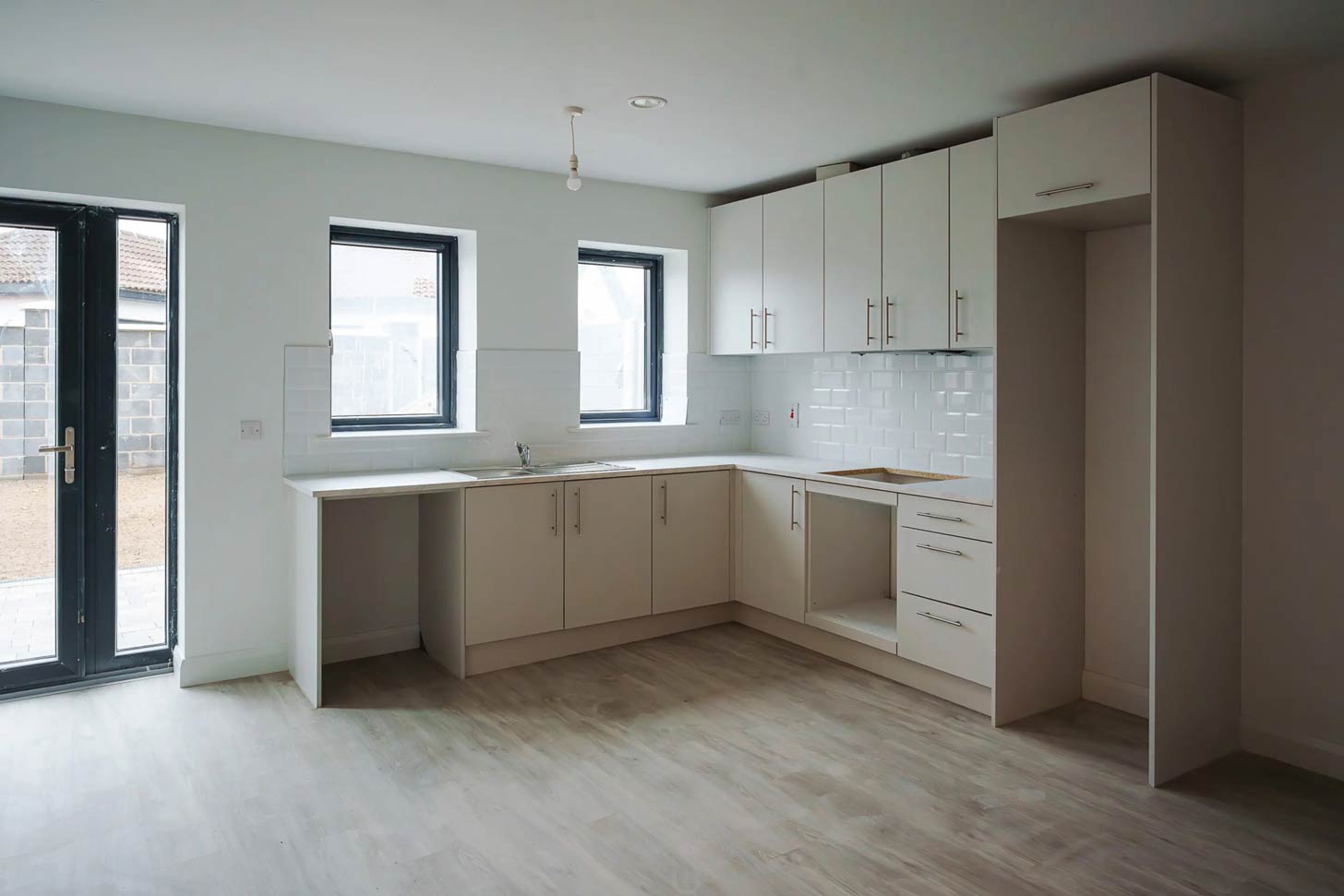
It’s a success that will surely have ripple effects.
“As the first 3D-printed social housing project in Europe, the Grange Close development sets a precedent for future housing solutions,” a press release from HTL.tech explained. “With countries like Sweden and Germany also experimenting with 3D-printed homes, this technology is poised to become a standard approach for addressing housing shortages.”
The statement also added that governments across Europe may increasingly adopt 3D printing to “deliver faster, more cost-effective housing solutions for low-income residents.”
“This project not only showcases the potential for rapid, sustainable construction but also serves as a blueprint for other nations facing similar challenges,” the statement concluded. “As 3D printing technology evolves, its role in shaping the future of housing construction looks increasingly promising.”
Header image courtesy of COBOD